Hermetic Seal Pins
FAQ: Can you help us design a more economical solution for our hermetic seal pin application?
Yes, absolutely. Because we focus on manufacturing the feedthrough and connector pins only, versus the entire glass-to-metal seal assembly, we’re able to recommend processes, materials or design tweaks that can result in substantial savings on your parts.
Custom part configurations
Feedthrough and connector pins for hermetic sealing applications have been around for close to 50 years; therefore, many of the configurations have become standardized.
However, customers often want to know if another type of configuration can be used – either to suit a unique application or to save on costs.
Figure 1, for example, shows two types of connector pin configurations: a hook and flat end that’s been pierced. Both pins serve the same purpose – wire attachment – but depending on the material, quantities, wire diameter, etc., one configuration could cost less.
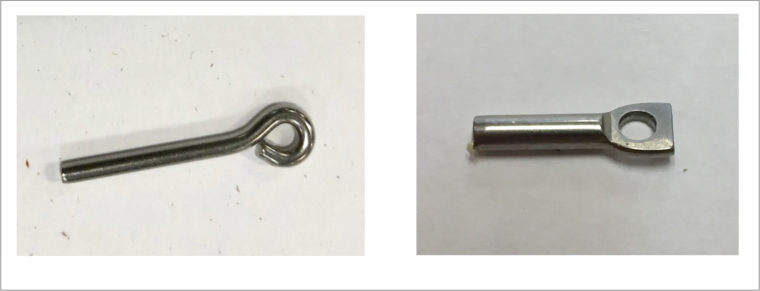
Figure 1: Two types of hermetic connector pin configurations: hook and pierced/flat
Processes improvements
One customer had been paying $40 per thousand for the micro switch brass pins in Figure 2. Working with the customer, we recommended changing from a Swiss screw machining process to cold forming – a less costly process where the wire is “displaced” or shaped, rather than machined.
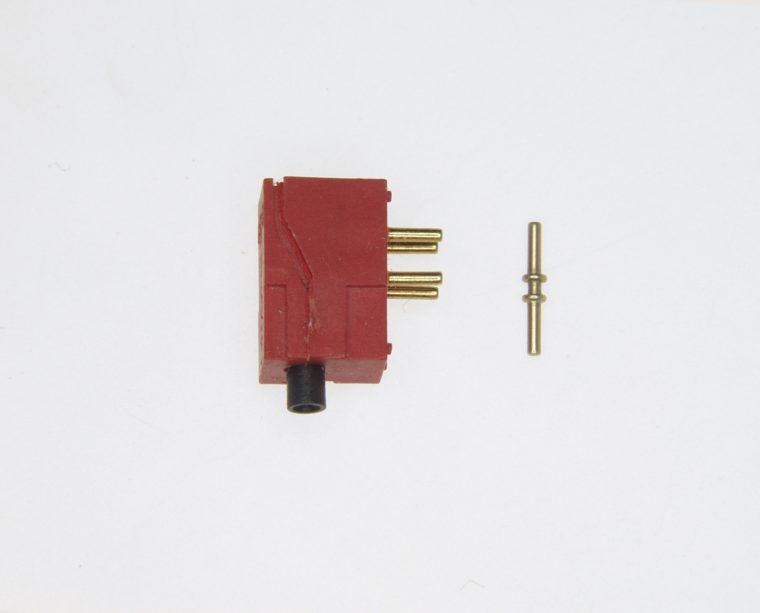
Figure 2: Micro switch brass pins manufactured using a cold forming process
The customer is now saving almost 80% per thousand for the pins, which feature the two cold formed “upsets.”
In another example, a customer wanted an .040 (shank diameter) headed feedthrough pin (a pin that looks like a nail) with a 0.160” head.
The rule of thumb when cold forming a head for this type of pin is to double the diameter of the wire – e.g. from 0.040” to 0.80”.
The customer, however, wanted a 0.160” diameter head, which meant we couldn’t make the pin using cold forming. Instead, we would have to use a machining process where excess material was removed to create the head.
To help you save on costs, we give you alternatives and then explain why one process costs more than another. Depending on how your part is being used and where, we can often recommend less expensive alternatives.
Material recommendations
For defense-related hermetically sealed parts, the pin material usually can’t be changed.
If the feedthrough or connector pins are for a commercial product, however, Form Cut can recommend materials that lower costs.
A customer was purchasing cold rolled steel for a part, due to its low cost per pound, but the material would rust. He therefore had to get the parts nickel-plated, for esthetic purposes.
After contacting Form Cut, we recommended he use stainless steel. Although the material cost a little more per pound, its use would allow him to remove the plating step, thus saving money and time in the long run.
When contacting Form Cut about your hermetic feedthrough or connector pin application, please let us know as much as possible:
- Where and how the part is being used
- Material needed
- Manufacturing process (e.g. how the part will be assembled)
- CAD drawing or photo / dimensions
- Price you’re currently paying or budget
- Etc.
Our engineers can help you tweak designs, recommend process improvements or help you choose materials the cost less but still meet specifications.